Comprehending What is Porosity in Welding: Causes and Solutions
Porosity in Welding: Identifying Common Issues and Implementing Finest Practices for Prevention
Porosity in welding is a prevalent issue that often goes undetected until it creates significant problems with the honesty of welds. In this discussion, we will certainly discover the crucial factors adding to porosity development, examine its damaging effects on weld performance, and talk about the best methods that can be adopted to reduce porosity event in welding processes.
Typical Reasons of Porosity
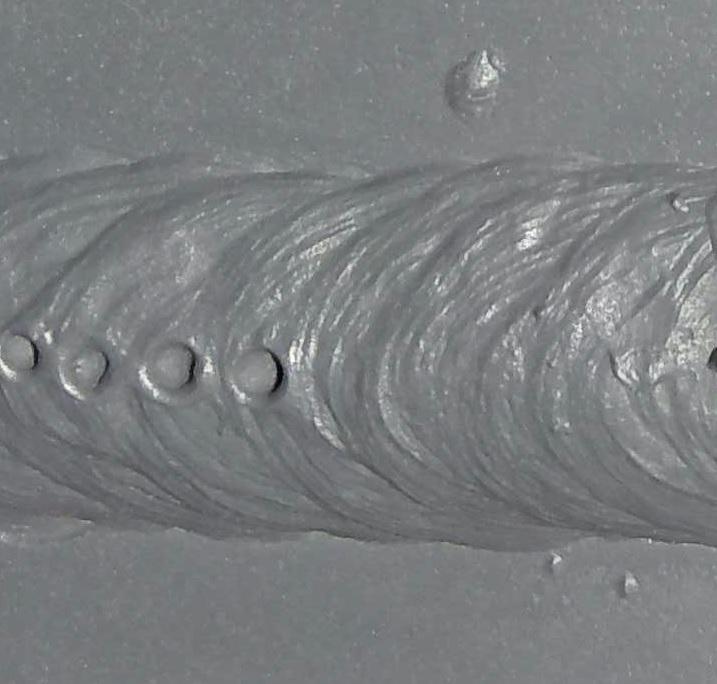
Using dirty or damp filler products can introduce impurities right into the weld, adding to porosity issues. To mitigate these typical causes of porosity, thorough cleansing of base steels, proper securing gas choice, and adherence to ideal welding parameters are crucial techniques in accomplishing top quality, porosity-free welds.
Impact of Porosity on Weld Top Quality

The existence of porosity in welding can considerably endanger the structural honesty and mechanical properties of bonded joints. Porosity creates voids within the weld steel, deteriorating its overall toughness and load-bearing capacity. These spaces act as stress and anxiety focus factors, making the weld much more susceptible to fracturing and failure under used loads. Furthermore, porosity can lower the weld's resistance to rust and various other environmental aspects, further decreasing its long life and performance.
Welds with high porosity levels often tend to show reduced effect strength and reduced ability to flaw plastically prior to fracturing. Porosity can hinder the weld's ability to effectively send pressures, leading to premature weld failure and possible security risks in crucial structures.
Best Practices for Porosity Avoidance
To improve the structural integrity and top quality of welded joints, what particular measures can be executed to lessen the event of porosity throughout the welding process? Porosity avoidance in welding is critical to make sure the integrity and toughness of the last weld. One effective technique is appropriate cleaning of the base steel, removing any kind of pollutants such as corrosion, oil, paint, or wetness that could cause gas entrapment. Guaranteeing that the welding equipment is in good condition, with tidy consumables and proper gas circulation rates, can additionally substantially reduce porosity. Furthermore, maintaining a steady arc and controlling the welding specifications, such as voltage, existing, and travel rate, helps produce a consistent weld additional reading pool that decreases the risk of gas entrapment. Making use of sites the appropriate welding method for the specific material being bonded, such as adjusting the welding angle and gun placement, can even more protect against porosity. Regular assessment of welds and immediate remediation of any type of issues determined throughout the welding procedure are important techniques to prevent porosity and create high-quality welds.
Relevance of Correct Welding Strategies
Applying appropriate welding techniques is extremely important in making sure the structural honesty and high quality of bonded joints, developing upon the structure of efficient porosity prevention procedures. Excessive warmth can lead to boosted porosity due to the entrapment of gases in the weld pool. Additionally, utilizing the appropriate welding specifications, such as voltage, current, and take a trip speed, is critical for accomplishing sound welds with marginal porosity.
Additionally, the selection of welding process, whether it be MIG, TIG, or stick welding, must straighten with the particular needs of the project to make sure optimum results. Correct cleansing and preparation of the base steel, along with selecting the ideal filler product, are also necessary parts of competent welding strategies. By sticking to these best methods, welders can lessen the threat of porosity formation and create top notch, structurally audio welds.
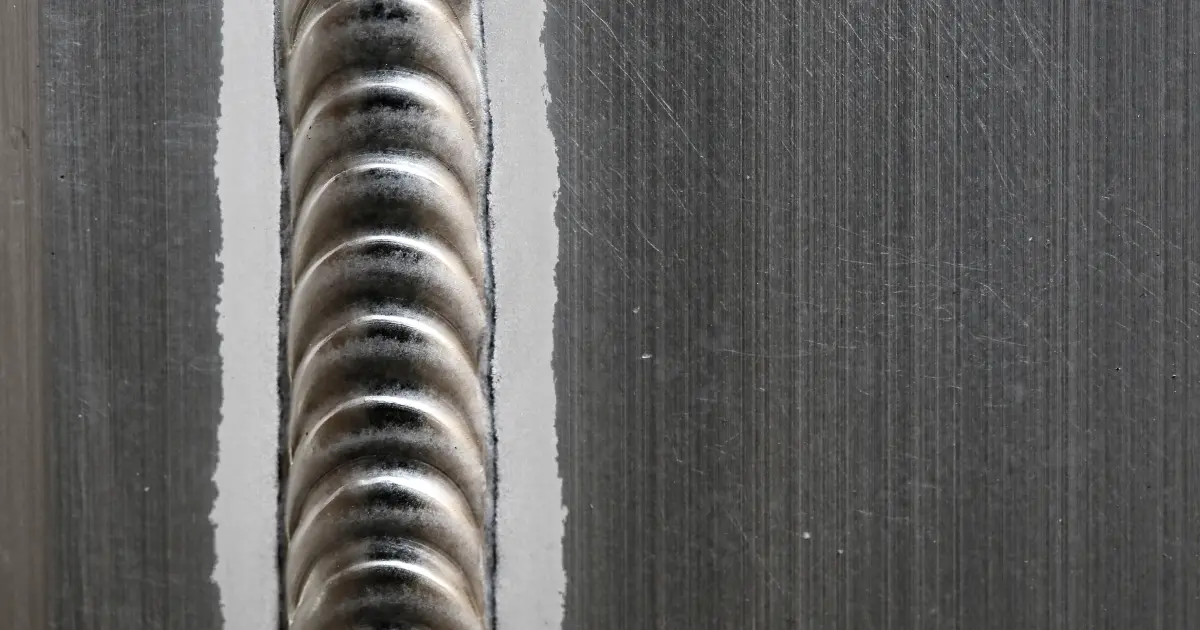
Checking and Quality Assurance Measures
Quality assurance actions play an important duty in verifying the integrity and dependability of read here bonded joints. Examining procedures are vital to discover and avoid porosity in welding, guaranteeing the stamina and sturdiness of the end product. Non-destructive screening methods such as ultrasonic testing, radiographic testing, and visual evaluation are frequently used to recognize possible issues like porosity. These techniques allow for the assessment of weld quality without compromising the integrity of the joint. What is Porosity.
Carrying out pre-weld and post-weld evaluations is also crucial in maintaining top quality control requirements. Pre-weld inspections entail confirming the materials, tools settings, and cleanliness of the workspace to stop contamination. Post-weld assessments, on the other hand, assess the last weld for any type of defects, consisting of porosity, and verify that it meets specified criteria. Carrying out a comprehensive top quality control plan that consists of comprehensive screening procedures and examinations is critical to lowering porosity problems and making certain the general top quality of welded joints.
Verdict
Finally, porosity in welding can be a typical problem that influences the quality of welds. By identifying the typical reasons for porosity and carrying out ideal techniques for prevention, such as proper welding methods and testing procedures, welders can make certain excellent quality and dependable welds. It is necessary to focus on avoidance approaches to decrease the event of porosity and keep the honesty of bonded frameworks.